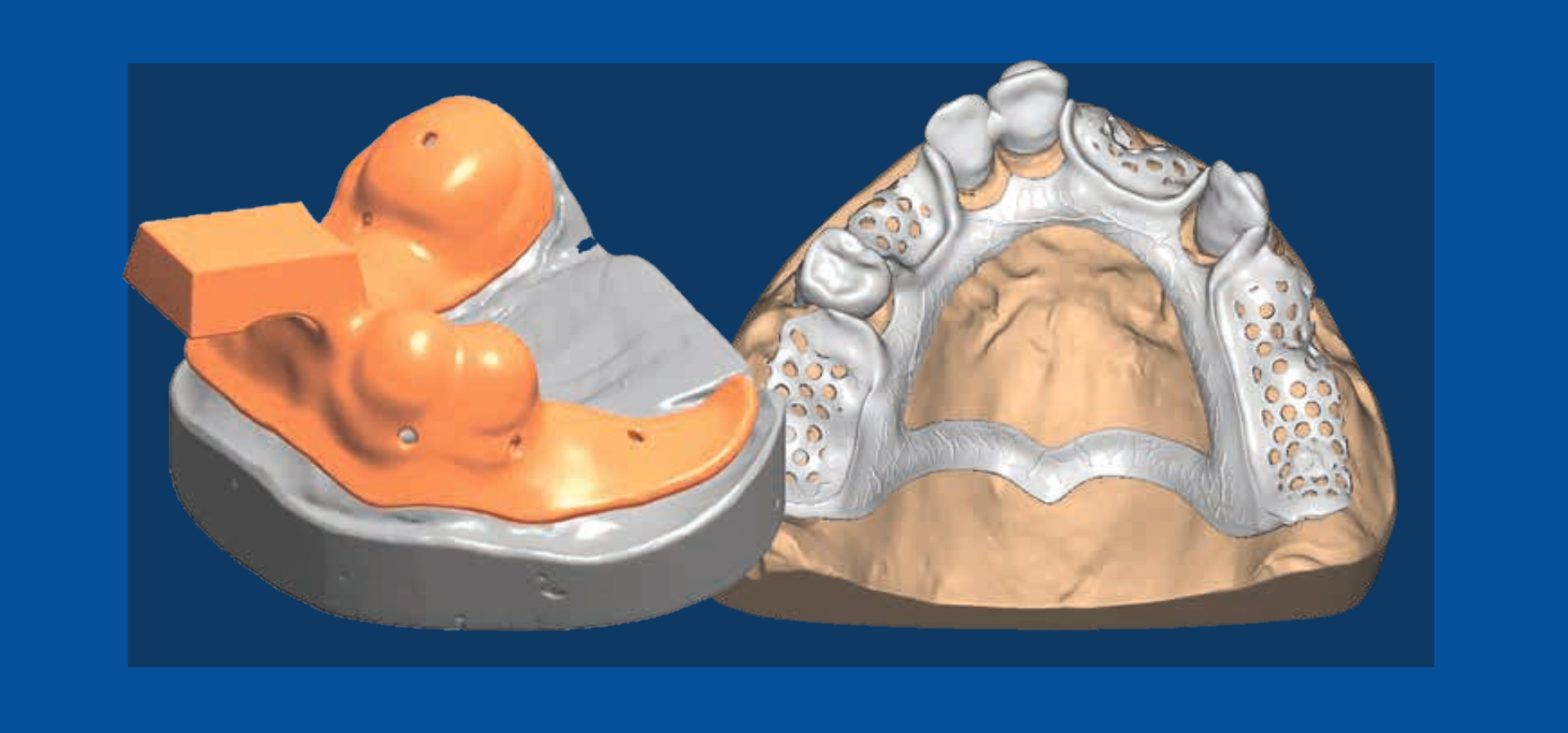
Intraorales Scannen und der digitale Workflow
In den letzten Jahren haben wir das Thema „Intraorale Abformung“ intensiv kennenlernen dür- fen. Nur durch enge Zusammenarbeit und den partnerschaftlichen Umgang mit unseren Kunden konnte dieser Weg gelingen. Heute sind wir stolz darauf, bis zu 50 Prozent unserer Aufträge digital zu erhalten. Die Etablierung des Intraoralscannens hat viele Vorteile mit sich gebracht, aber es gab und gibt auch bei Nutzung dieser Technik Hürden zu bewältigen.
Der vorliegende Beitrag vermittelt einen Einblick in unsere Erfahrungen mit dem digitalen Workflow und gibt Plus- und Minuspunkten dabei gleichermaßen Raum.
Die digitale Abformung
Zu Beginn des prothetischen Workflows steht die Abformung. Sie bildet die Arbeitsgrundlage, auf der alles weitere aufbaut, und entscheidet bereits über Erfolg oder Misserfolg der zahntechnischen Versorgung.
Viele unserer Kunden blicken auf langjährige Erfahrungen in der klassichen Zahnmedizin zurück. Da ist es praktisch, dass die Vorbereitung eines Intraoralscans sehr dem Vorgehen bei analoger Abfor- mung ähnelt. Auch bei digitaler Abformung ist eine gute Vorbereitung unerlässlich, da – zumindest momentan noch – nur gescannt werden kann, was auch optisch zu erfassen sprich sichtbar ist. Dann aber verändert sich der Workflow und muss entsprechend neu erlernt werden. Essenziell ist das Einhalten der vorgegebenen Scanstrategien der Hersteller. Und speziell am Anfang ist es wichtig, auf Kleinigkeiten zu achten und das Auge auf mögliche Scanfehler zu schulen. Schließlich besteht bei Durchführung einer digitalen Abformung die Chance, erkannte Fehlstellen direkt auszubessern. Sind die einzelnen Kiefer erfolgreich gescannt, folgt noch eine nicht unwesentliche Herausforderung: Um am Ende der zahnärztlichen Behandlung einen der größten Zeitvorteile der digitalen Abformung nutzen zu können, müssen die Kiefer nun richtig zueinander verschlüsselt werden..
Im Vergleich zur klassischen Abformung hat der Anwender im digitalen Workflow bereits jetzt Eigen- beweglichkeiten, Gipsexpansionen und Abdruckrückstellungen als mögliche Fehler ausgeschlos- sen. Das spätere Einschleifen der prothetischen Versorgung wird damit auf ein Minimum reduziert.
Die entstandenen digitalen Daten sind oftmals sehr umfangreich und müssen korrekt und Daten- schutz-konform an das zuständige Dentallabor übermittelt werden. Auch dieser Punkt stellt in vielen Fällen durchaus eine Hürde dar. Es darf von Zahnarztpraxen nicht als Selbstverständlichkeit betrach- tet werden, dass ihr zahntechnisches Labor jedes am Markt vorhandene Datenformat unmittelbar verarbeiten kann. Ein aktiver Austausch im Vorfeld ist daher unverzichtbar; hier zählt einzig und alleine Teamwork.
Pro | Contra |
kein Würgereiz oder Erstickungsängste | anfängliche Misserfolge möglich |
hoher Komfort für den Patienten | verlassen der jahrelangen Routine |
Geschwindigkeit | Abformung muss weiterhin gut vorbereitet werden |
direktes Ausbessern von Scanfehlern | Personal muss neu geschult werden |
keine Abdruckrückstellung | schnelle Internetverbindung nötig |
keine Gipsexpansion | Investitionen in Praxis und Labor sind nötig |
Eigenbeweglichkeit der Zähne mit einbezogen | |
weniger Einschleifen | |
steile Lernkurve gemeinsam neue Wege gehen |
Empfang einer digitalen Abformung
Nach erfolgreichem Datenversand an das Dentallabor beginnt hier die Verarbeitung der Rohdaten. Die Mehrzahl der Oralscans werden im STL-Format und zusätzlich in Farbe übermittelt. Beides hilft dem Zahntechniker die Qualität des Scans zu überprüfen. Softwareseitig gibt es mehrere Lösungen, welche sich im Ablauf aber wenig voneinander unterscheiden. Der digitale Weg unterscheidet sich vom analogen, indem der Zahnersatz ohne physisches Modell konstruiert wird.
Das zahntechnische Modell wird erst nach Abschluss des Computer Aided Designs der protheti- schen Versorgung erstellt. Für die Herstellung des Arbeitsmodells wird eine zusätzliche Modellbuil- der-Software benötigt. Die digitale Modellherstellung ist für Viele noch Neuland. Im Anschluss an die Konstruktion wird dafür bestimmt:
- welche Stümpfe herausnehmbar sind
- die Freistellung von Nachbarzähnen
- ob es ungesägte Kontrollmodelle gibt
- ob eine Zahnfleischmaske benötigt wird
- welche Modellanaloge verwendet werden
- wie der Biss verschlüsselt wird
- die Beschriftung des Modells
- das Aushöhlen des Modells (Druckvorbereitung)
Der Modelldruck
Nach Abschluss des CAD-Prozesses erhält der Zahntechniker zwei Datensätze zur weiteren Verarbei- tung: einen für den Zahnersatz und einen für das dazugehörige Modell zum 3D-Drucken. Anfänglich haben wir das Thema 3D-Druck unterschätzt. Zu Beginn gab es Schwankungen und Probleme in folgenden Bereichen:
- Erstellung von demensionstreuen Modellen
- Passungen der Einzelstümpfe und Nachbarzähne
- Okklusionsungenauigkeiten
- Wiederholungsungenauigkeiten
- Materialgüte der Modelle
- Umfang des Nachbearbeitungsprozesses nach dem eigentlich Druckvorgang
- Entfernen von Stützstrukturen
- Entfernen von Dispersionsschichten
- Lichthärteprozess
- die richtige Entsorgung der verwendeten Resine
- Einhaltung von Arbeitsschutz- und Verarbeitungsrichtlinien
- negative Beeinflussung durch Sonneneinstrahlung
Da unserer Meinung nach ein qualitativ hochwertiges Modell in der Zahntechnik unverzichtbar ist, haben wir in den letzten Jahren keine Kosten und Mühen gescheut, um diesen Prozess ständig zu optimieren. Hierzu war es nötig in verschiedene Systeme zu investieren und aus den Fehlern zu lernen. Heute beherrschen wir einen gleichbleibenden Prozess und können so alle digitalen Vorteile der Zahntechnik ausschöpfen.
Pro | Contra |
Zeitersparnis bei der Modellherstellung | Schulung von Personal |
höhere Präzision durch Wegfall vieler einzelner Arbeitsschritte | Investitionen in Software |
keine Übertragungsfehler | Abhängigkeit von Druckzentren oder Investition in 3D-Drucker |
Farbscans helfen bei der Festlegung der Präparationsgrenzen | anfängliche Misserfolge bei Einarbeitung |
Die farbliche Darstellung des Zahnstumpfes hilft enorm bei der Auswahl transluzenter Materialien | viele verschiedene Systeme und Dateiformate |
Herstellung eines Alveolarmodells zur besseren Ausformung des Zahnfleischsaums | Abstellung von Fachpersonal zur Modellherstellung |
Platzsparende Archivierung von Modellen in Form eines Datensatzes | |
Modelle bei Bedarf auch nach Jahren neu ausdruckbar |
Chancen und Möglichkeiten im zahntechnischen Labor
Nach der erfolgreichen Herstellung der 3D-gedruckten Modelle und der CAD/CAM-gefertigten zahntechnischen Versorgung beginnt der handwerkliche Teil der Arbeit. Für Anfänger empfiehlt es sich, mit einer Einzelkrone bzw. kleinen Brücke zu beginnen. So können Praxis und Labor die Mög- lichkeiten des neuen Workflows schonend und mit ersten Erfolgserlebnissen erlernen. Die Lernkurve ist vor allem bei den ersten Arbeiten sehr steil und motivierend. So stellt sich die Motivation, auch umfangreichere, komplexere Restauration zu fertigen, schon bald wie von selbst ein. Das können z. B. Einzelimplantatkronen oder kleinere Brücken sein.
Das Versorgen von Implantaten ist grundsätzlich sehr einfach, es sollten allerdings im Vorfeld folgende Eckpunkte geklärt werden:
- Welche Scanbodys nutze ich als Behandler und kann mein Labor mit den hier erstellten Daten arbeiten?
- Besteht bereits von Seiten der Hersteller ein Workflow für digitale Modellherstellung?
- Gibt es Modellanaloge und Zubehör für die gewünschte Indikation?
Hier ist es unbedingt notwendig, frühzeitig verwendete Materialen, eingesetzte Scanbodys, Klebebasen, Preface Abutments und Modellimplantate aufeinander abzustimmen. In der Ver- gangenheit hat auch in der Implantologie ein starker Wandel stattgefunden. Die Fülle an ver- schiedenen Systemen und Herstellern lässt in Praxis und Labor viele unvorhersehbare Probleme entstehen. Auch für die Industrie ist dies immer noch Neuland. Das schnelle Wachstum der ver- schiedenen Anbieter führt leider noch zu Lücken in der Fertigungskette. Hat man sich hier aller- dings einmal aufeinander abgestimmt, steht einer zeitsparenden und erfolgreichen Zusammen- arbeit nichts mehr im Wege. Selbst größere Implantatfälle sind mit etwas Übung zügig umsetz- bar. Aus betriebswirtschaftlicher Sicht macht es Sinn, spezielle umfangreiche Indikationen mit dieser Technik zu versorgen.
Mittlerweile ist es uns möglich, auch herausnehmbaren Zahnersatz zeitsparend und kosteneffizient computergestützt zu fertigen. Anders als bei der klassischen Abdrucknahme werden alle erforderli- chen Daten für die Versorgung bereits in der ersten Sitzung erfasst. Diese Vorgehensweise ermög- licht es uns, Überabformung und Bissnahme einzusparen, und somit auch, viele mögliche Fehler auf beiden Seiten zu vermeiden. Bei gewissenhafter Vorbereitung des Mundscans ist es denkbar, bereits nach der digitalen Abformung eine Gesamtanprobe des Zahnersatzes zu liefern. Besonders hier sehen wir die Stärken der neuen digitalen Techniken. Gesicherte und gleichbleibende Prozesse verbessern in Praxis und Labor Abläufe und Kosteneffizienz. Durch diese uns neu gegebenen Tools sehen wir einen deutlichen Wandel in den nächsten Jahren, welcher für die deutsche Zahntechnik viele große Chancen mit sich bringt.
Pro | Contra |
sichere Prozesse | erforderliches Know-how der einzelnen Arbeitsschritte muss erlernt werden |
Einsparung von Sitzungen in der Praxis | digitale Workflows auch seitens Industrie nicht immer schon ausgereift |
mehr Zeit im Labor durch weniger Termine und direkte Gesamtanproben | je nach Ausstattung des Labors / der Praxis auf externe Partner angewiesen |
weniger mögliche Fehlerquellen durch Vermeidung von zusätzlichen Überab formungen und Bissnahme | |
hohe Rentabilität der eingesetzten digitalen Techniken |
Patienten schätzen die digitale Abformung aus den bekannten Gründen erfahrungsgemäß sehr:
- maximaler Patientenkomfort
- kein Würgereiz oder Erstickungsängste
- sofort überprüfbare Ergebnisse
- bequem und zeitsparend in nur einer Sitzung
- höchste Präzision
- schnelle digitale Abformung von Ober- und Unterkiefer
Andreas Rawe
- 2002 Ausbildung zum Zahntechni- ker
- 2006 – 2010 Anstellung im Dental- labor Leifhelm in Beckum; Schwer- punkt Kunststoff und Modellguss
- 2010 – 2011 Anstellung im Den- tallabor Borgmeier in Wadersloh; Schwerpunkt Gerüstherstellung
- 2011 Anstellung im Dentallabor Borghorst in Gescher; Schwer- punkt Kombitechnik, Keramik und CAD/CAM
- seit 2014 Technische Leitung und Kundenbetreuung bei CreaCam Frästechnik GmbH & KG
- regelmäßige CAD/CAM-Fort- bildungen
ZTM Michael Borghorst
- 2002 Ausbildung zum Zahntechniker
- 2006 Besuch der Meisterschule in Münster
- 2007 Einstieg in das Familienunter- nehmen Dentaltechnik Borghorst, gegründet 1993 vom Vater Andreas Borghorst
- seit 2008 Tätigkeit als Referent für bredent (Compositeverblendun- gen, digitaler Workflow)
- 2014 Gründung von CreaCam Fräs- technik GmbH & KG, Dienstleis- ter für Frästechnik und 3D-Druck
- 2018 Curriculum CAD/CAM an der TU München (Prof. Dr. Daniel Edelhoff)
- 2019 Fertigstellung des neuen Labors / Fräszentrum in Gescher Verabschiedung von Andreas Bor- ghorst in den Ruhestand; Neugrün- dung der Zahntechnik am Campus GmbH & KG zusammen mit Philipp Weishaupt, ehemaliger Inhaber von Zahnwerkstatt Weishaupt
Kontakt
W.B. Zahntechnik
am Campus GmbH & Co. KG Am Campus 15
D-48712 Gescher
Tel. +49 (0) 2542 / 98 29 3